Mastering Product Availability: Strategies to Optimize Inventory and Meet Demand
Our Clients
Committing to the success of our clients around the world
What is product availability?
Product availability refers to the status of a product indicating whether it is in stock and ready for purchase or use. It reflects the current inventory levels of a product and whether it can be immediately obtained by customers.
Why is product availability important?
Product availability is critical for any company aiming for successful sales. When a product is available, customers can easily purchase it, leading to increased revenue. Conversely, a lack of stock can cause customer frustration, lost sales, and even damage the brand’s reputation.
Explaining Product Availability
There is ongoing debate about how much inventory should be held. Sales teams want high product availability to meet customer demand, while finance departments aim to minimize working capital investment and reduce costs. This creates a conundrum, but one thing is clear: running out of stock is a major problem.
NO STOCK = NO SALE NO SALE = NO CASH!!!
As inventory expert Tony Wild once said, “Inventory is the result of lack of data.” However, a lack of inventory can be just as problematic. Poor data, lack of focus, insufficient time, inefficient processes, and communication issues often cause product availability problems.
Common Challenges in Product Availability
Here are some common challenges businesses face regarding product availability:
- Supply Chain Bottlenecks: Delays in the supply chain can prevent timely restocking.
- Unexpected Customer Orders: Sudden spikes in demand can quickly deplete inventory.
- Forecast Errors: Inaccurate demand forecasts can lead to either stockouts or overstock.
- Supplier Issues: Problems with suppliers, such as delays or quality issues, can impact product availability.
- Missing Data: Incomplete or inaccurate data can hinder effective inventory management.
- Angry Customers: Customer dissatisfaction can escalate when products are unavailable.
- Supplier Payment Issues: Financial problems with suppliers can disrupt the supply chain.
- Disrupted Processes: Inefficient processes can lead to delays and errors in inventory management.
Strategies to Improve Product Availability
Tip 1: Identify Urgent vs. Important Availability Issues All tasks can be categorized into two main categories:
- Important: Tasks that help achieve specific goals, such as reviewing forecast exceptions to improve inventory management.
- Urgent: Tasks that require immediate attention but may not directly impact long-term goals, like placing a last-minute order to fulfill a customer promise.
Tip 2: Use the Covey Matrix Based on President Eisenhower’s principles, Stephen Covey developed the Covey Matrix to help prioritize tasks:
- Important and Urgent: Do these tasks immediately.
- Important but Not Urgent: Schedule these tasks.
- Not Important but Urgent: Delegate these tasks if possible.
- Not Important and Not Urgent: Eliminate these tasks.
Tip 3: Apply Management by Exception Automate repetitive and low-value tasks, allowing your team to focus on critical issues requiring human intervention. This approach helps manage exceptional situations and prevents stockouts and overstock.
Tip 4: Collaborate and Adjust Forecasts Work with sales and marketing teams to adjust forecasts based on market intelligence. Consider factors like upcoming promotions, new customer acquisitions, and changes in demand patterns.
Effective product availability management involves balancing sufficient stock levels to meet demand with minimizing excess inventory. Prioritizing tasks, automating where possible, and collaborating across departments can improve product availability and enhance overall supply chain performance.
For a deeper understanding of market strategies, check out our guide on product positioning and our article on product visibility for strategies to boost your product’s presence on the shelf.
Success Stories
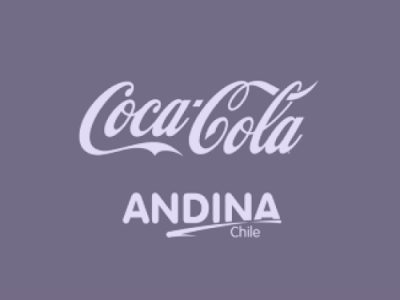
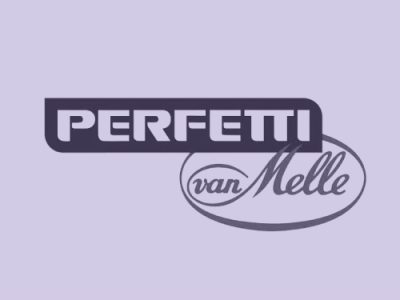
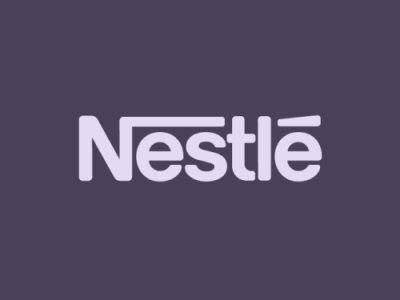
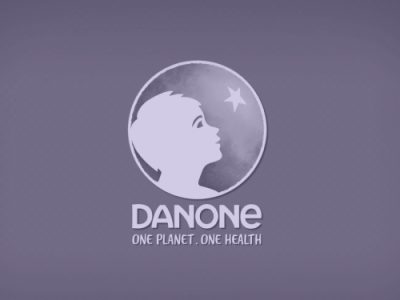
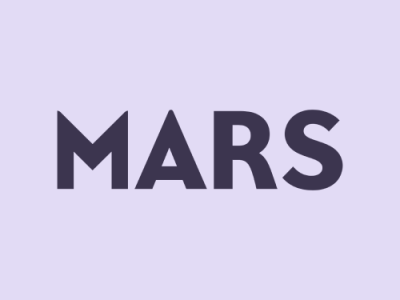
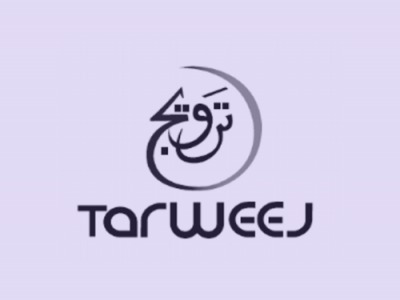
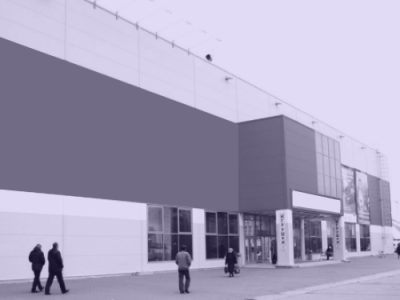
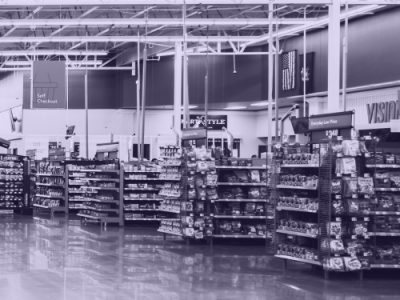
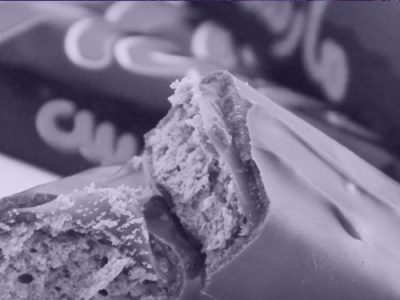
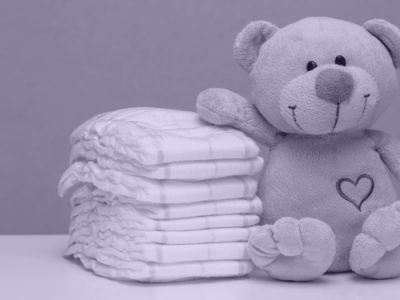
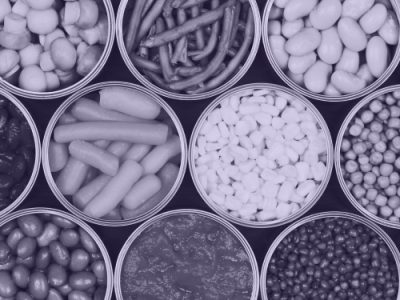
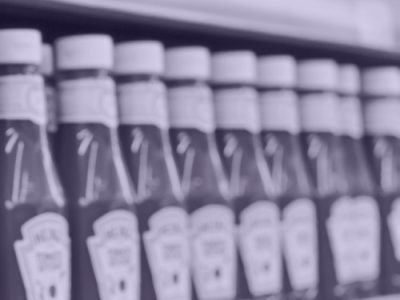
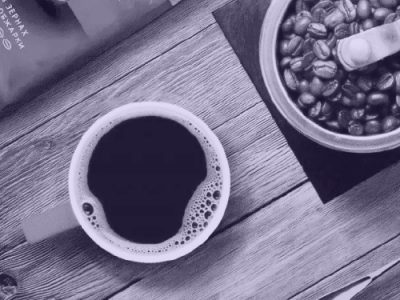
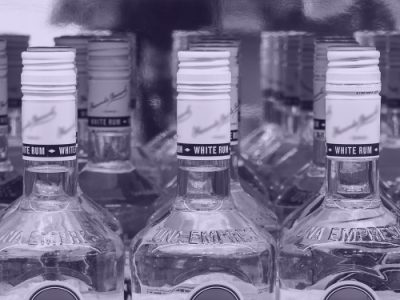
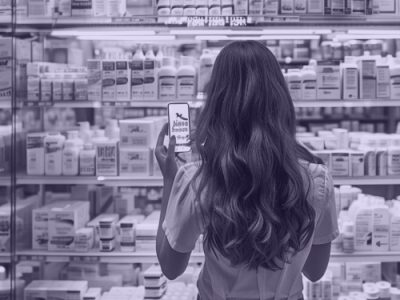
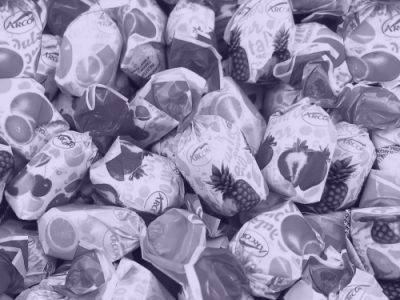
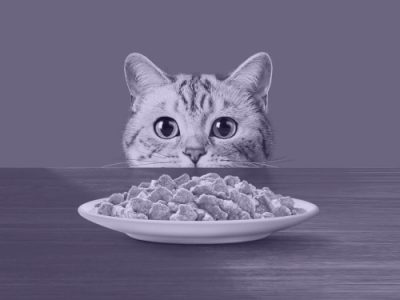
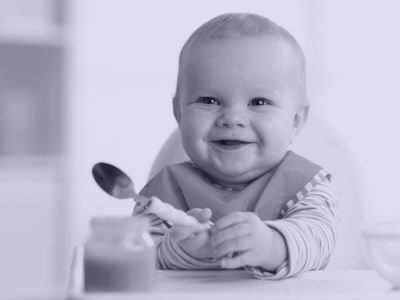
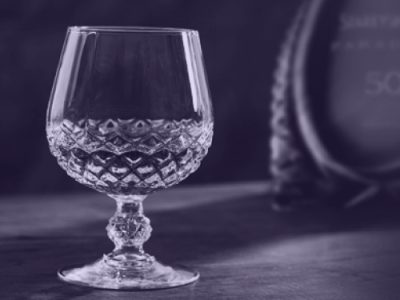
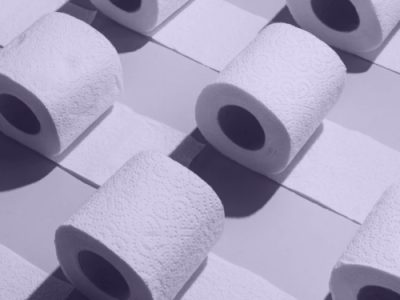
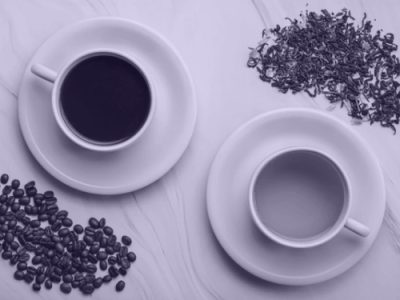